SootGone™ - a Unique Online Soot Cleaning System
for Industrial Boilers, Heaters and Incinerators
SootGone™ soot blower is based on detonation-pulse phenomenon and has been developed with deep understanding of detonation processes to keep your boiler clean and operating at full capacity and efficiently without disruption or downtime. SootGone™ has overcome the shortcomings of conventional on-line soot cleaning devices that today's market can offer.
The main highlight is the use of aerodynamic forces to provide high dynamic pressure instead of using compressors or high pressure fuel gas cylinders. The SootGone™ system doesn't have pistons, sealings, and moving parts. There is no wear and tear which ensures high reliability and low maintenance costs.
There is no need to keep a huge amount of spare parts in stock, the cost of which can reach hundreds of thousands of dollars.
The SootGone™ system can be applicable in the following areas:
-
evaporators
-
economizers
-
superheaters
-
air preheaters
-
ducts
-
hoppers
-
chimneys
As well as being effective in hard-to-reach areas, the Soot Gone™ system can be used in corrosive environments.
The SootGone™ system can be used for removal of the following sedimentation types:
-
ash
-
soot
-
slag
-
cement
-
lime
-
pigments
-
additives
-
fertilizers, etc.
The SootGone™ system is characterized by the following attractive features:
-
maximal efficiency compared to the conventional steam soot blowers, rappers, air-blowers, etc.;
-
no moving parts, hence very reliable with minimal maintenance;
-
small footprint;
-
flexible, easy and cheap installation, can be installed in arduous places;
-
necessary utilities: atmospheric air and low pressure (3 Bar) fuel gas (normally Methane or LPG);
-
no need for electrical or instrumentation cables along the boiler itself;
-
no need for huge service platforms installed on the structure of steam generators;
-
minimal operation cost ;
-
user-friendly;
-
safe for the pipes, structure, refractories of the boiler and any burning equipment;
-
safe for personnel and the environment;
-
meets safety codes and standards.
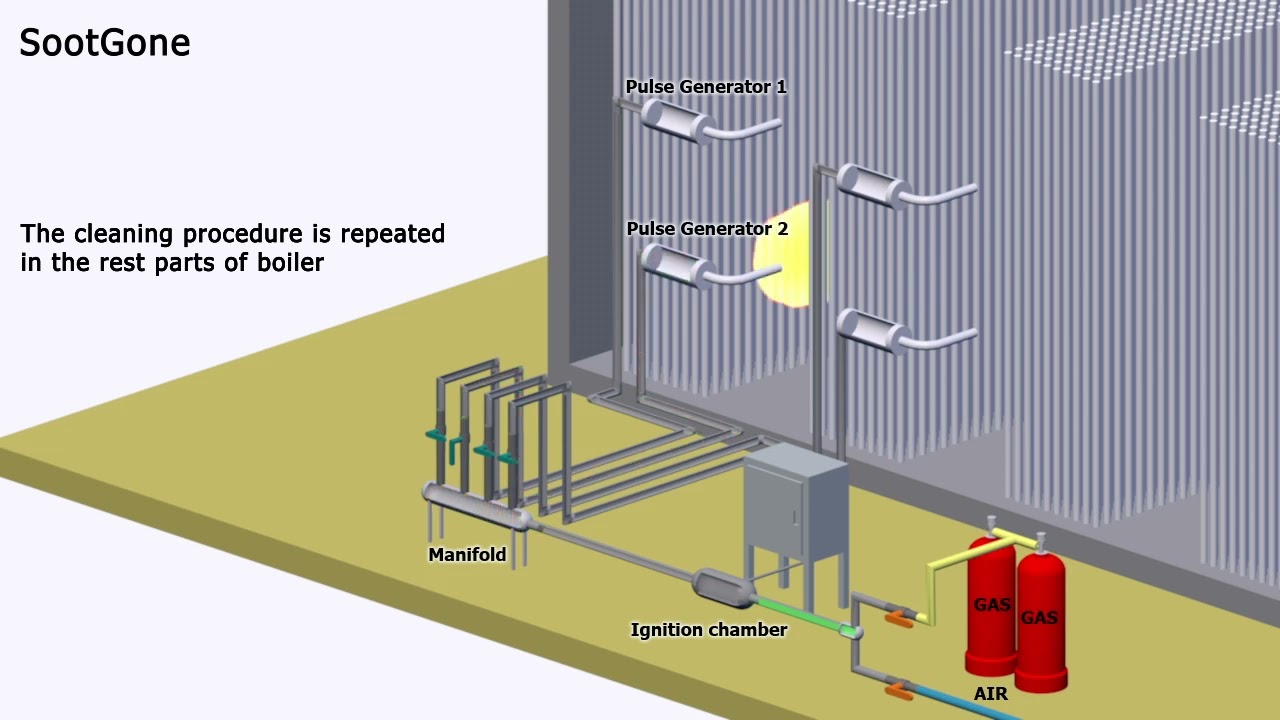
SootGone™ System is similar to an octopus which has one head and numerous tentacles.
The head of the SootGone™ is the control block (Flame Front Generator) and its tentacles are the numerous Pulse Generators that are stationary installed on the boiler.
The FFG is equipped with all the necessary instrumentation and can activate several pulse generators one after the other.
The Procedure of SootGone™ Cleaning Process

Stage 4: Creating the Pulse in the Pulse Generator No.1